resistance welding control_e_product_SK54
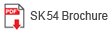
– Secondary feed-back constant current control
– Self-adjustment for maximum current
– 15 Weld schedules
– External schedule select
– Spot, twin head spot and seam welder compatibility
– 3 Impulse weld schedules(weld2 is half cycle control)
– Up and down slope
– 9 Steppers / Linear stepper
– 2 Pressure valve output and 7 operations
– Current1,2,3 monitor with high/low monitor
– 3 easy-to-operate counters to aid in systematic quality control and tipdressing schedules
– PC and RS485 network interface
PC and RS485 Network Interface
By using welding data logger(Fcom_V2.3) software, welding data can be collected from each SK54 controller at real time and the collected data can be stored by excel file at computer.
– One PC can be linked to maximum 32 units of SK54.
– Weld current data and schedule data can be requested to each of SK54, then the data can be seen and printed.
– Weld schedule can be changed by PC.
– When welding defects is occurred, event monitoring is available and time and weld current data can be checked easily at real time.
– Opto-Isolated RS485 card(optional) is installed inside of SK54.
– PC and SK54 is connected by 2 electric wires and the length is maximum 1.2 Km.
Do you have any questions about the SK54?